Products & Services

.png)
REGISTER SYSTEMÂ
In the context of machine automation, a "Register System" typically refers to a mechanism or component that is responsible for accurately registering or detecting the position, alignment, or presence of objects, parts, or materials within a system or process.
Here are a few examples of how a Register System might be used:
-
Printing Industry: In printing presses or packaging machines, a Register System ensures precise alignment of colours or graphics by detecting and adjusting the position of substrates or printing plates.
-
Conveyor Systems: In manufacturing or logistics, a Register System may be used to detect the presence of products on a conveyor belt and ensure they are properly positioned for further processing or packaging.
-
Quality Control: In automated inspection systems, a Register System can be used to verify the alignment or orientation of components to ensure they meet quality standards.
-
Material Handling: In warehouse automation, a Register System may be employed to accurately position pallets or containers for loading and unloading operations.
Overall, a Register System plays a crucial role in ensuring the accuracy, efficiency, and quality of various automated processes by providing real-time feedback on the position or presence of objects.
GUILOTINE MACHINE CONTROL SYSTEM
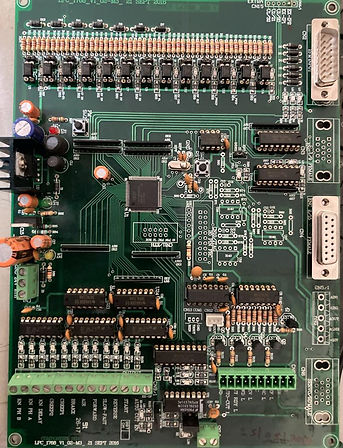
A "Guillotine Machine Control System" in machine automation refers to the control system used to operate a guillotine machine. A guillotine machine is a type of cutting equipment typically used in industrial settings for cutting materials such as paper, cardboard, plastics, and metal sheets.
The control system for a guillotine machine includes various components and functionalities aimed at automating and optimizing the cutting process. These may include:
-
Positioning Control: The system controls the position of the cutting blade with precision, ensuring accurate cuts according to specified dimensions.
-
Speed Control: It regulates the speed of the cutting blade to achieve efficient cutting while maintaining quality and safety.
-
Pressure Control: In certain applications, the control system may manage the pressure applied by the cutting blade to optimize cutting performance, especially when dealing with materials of varying thicknesses or properties.
-
Safety Features: The control system incorporates safety mechanisms to prevent accidents and ensure operator safety, such as emergency stop buttons, safety guards, and sensors to detect obstructions.
-
User Interface: The system typically includes a user-friendly interface, often in the form of a graphical user interface (GUI), through which operators can input cutting parameters, monitor the cutting process, and receive feedback or alerts.
-
Automation Capabilities: Advanced guillotine machine control systems may offer automation features such as programmable cutting sequences, batch processing, and integration with other equipment or systems in the production line.
Overall, the Guillotine Machine Control System plays a critical role in ensuring efficient, precise, and safe operation of guillotine machines in various manufacturing and processing industries.
POWER CONTROL SYSTEM
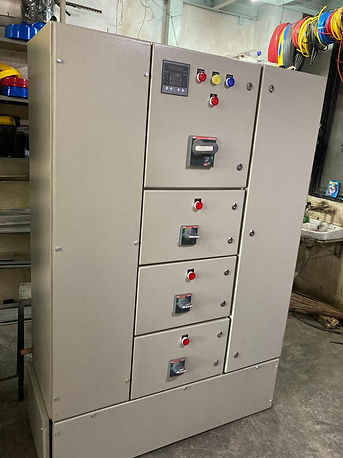
A "Power Control System" in machine automation refers to a system responsible for regulating and managing the electrical power supplied to machines or equipment within an industrial setting.
Here are some key aspects of a Power Control System:
-
Power Distribution: It involves distributing electrical power from the main power source (such as a grid connection or generator) to various machines and equipment throughout the facility.
-
Voltage Regulation: The system ensures that the voltage supplied to each machine or equipment is within acceptable limits to prevent damage and ensure proper operation.
-
Current Control: It regulates the flow of electrical current to match the requirements of different machines and processes, optimizing energy efficiency and preventing overloading.
-
Safety Features: Power Control Systems incorporate safety measures such as circuit breakers, fuses, and ground fault protection to protect equipment and personnel from electrical hazards.
-
Monitoring and Control: These systems often include monitoring and control capabilities to track power consumption, detect abnormalities, and adjust power distribution as needed to maintain optimal performance.
-
Automation Integration: In modern manufacturing environments, Power Control Systems may be integrated with automation systems to enable remote monitoring, control, and optimization of power usage based on production demands and energy efficiency goals.
Overall, a Power Control System plays a critical role in ensuring the reliable and efficient supply of electrical power to support the operation of machines and equipment in industrial automation applications.
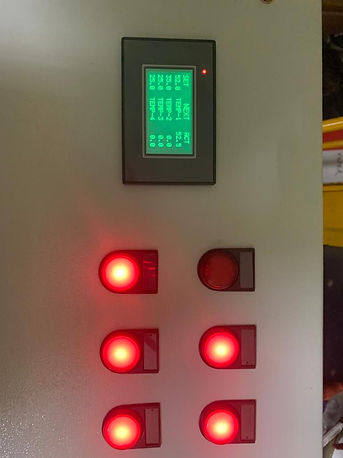
ROLLER HEATER SYSTEM
A "Roller Heater System" in machine automation typically refers to a system designed to heat rollers used in various industrial processes. These systems are commonly found in applications such as printing, laminating, embossing, and food processing.
Here's an overview of the key components and functionalities of a Roller Heater System:
​
-
Roller Units: These are the rollers that are heated as part of the system. They can vary in size, material, and configuration depending on the specific application requirements.
-
Heating Elements: Roller Heater Systems are equipped with heating elements positioned inside the rollers or in close proximity to them. These heating elements can be electric resistive elements, infrared heaters, or other types of heating technology.
-
Temperature Control: The system includes temperature control mechanisms to regulate the heat output and maintain the desired temperature of the rollers. This can involve thermostats, temperature sensors, and feedback control loops to adjust the heating elements as needed.
-
Insulation: To minimize heat loss and ensure efficient heating, Roller Heater Systems often feature insulation materials surrounding the rollers or heating elements.
-
Automation Integration: In automated manufacturing environments, Roller Heater Systems may be integrated with larger automation systems to enable seamless control and coordination with other equipment and processes.
Overall, Roller Heater Systems play a crucial role in industrial applications where precise and controlled heating of rollers is required to achieve desired outcomes in various production processes.
AUTO NUMBERING UNIT

In machine automation, an "AUTO NUMBERING UNIT" refers to a component or system that automatically assigns unique numbers or identifiers to products, parts, or items as they move through a production or assembly line.
Here's a breakdown of its functionalities:
-
Automatic Numbering: The unit is responsible for automatically generating and assigning sequential or unique numbers to items based on predefined criteria.
-
Integration with Production Line: It is typically integrated into the production line or machinery, allowing for seamless operation and synchronization with other automation components.
-
Data Capture: The auto numbering unit may capture relevant data associated with each item, such as timestamps, batch information, or product specifications, and incorporate this data into the assigned identifier.
-
Accuracy and Reliability: The system ensures the accuracy and reliability of the assigned numbers, minimizing errors and ensuring consistency in the identification process.
-
Versatility: Auto numbering units may be configurable to accommodate different numbering formats, patterns, or requirements based on the specific needs of the production process or industry standards.
Overall, an auto numbering unit plays a crucial role in streamlining production processes, enabling efficient tracking and traceability of products or components throughout the manufacturing cycle.